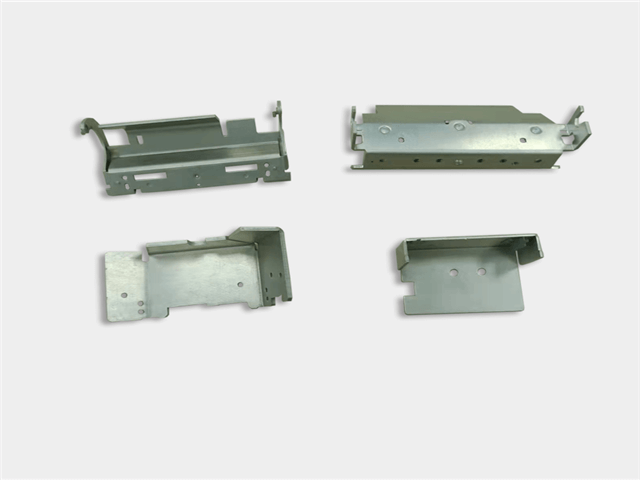
Metal stamping processing is a complex and intricate technique that involves various challenges and considerations. Among these, bending processing plays a crucial role in shaping the material to meet specific design requirements. In this article, we will delve into the intricacies of bending processes, focusing on factors such as spring back, punch and die gaps, fillet radii, and bending depth. By understanding and optimizing these factors, we can ensure precise bending outcomes while minimizing undesired spring back effects.
Bending and Spring Back
Bending is a critical step in metal stamping, to achieve precise bending, various tools and techniques are utilized. These include V-dies, radius tooling, air bending, bottoming, coining, and pre-bending, but it often results in spring back, where the bent metal tends to return to its original shape. Achieving precise bending and minimizing spring back is essential for maintaining dimensional accuracy.
Minimizing Spring Back
Spring back occurs due to the elastic properties of the metal. When the bending force is released, the metal tends to return to its original shape. Spring back can lead to dimensional inaccuracies and affect the overall quality of the stamped components, so we must control spring back when bending metal stamping parts.
Controlling Spring Back
Minimizing spring back requires careful considerations during the metal stamping process. Techniques such as over-bending, bottoming, and using anti-spring back devices can help reduce spring-back effects. Proper tool and die design, as well as material selection, play a significant role in controlling spring back.
Understanding Spring Back and its Relationship with Curvature
Spring back refers to the tendency of a material to return to its original shape after bending. This phenomenon can result in dimensional inaccuracies and hinder the achievement of desired shapes during metal stamping. It is essential to consider the relationship between spring back and the radius of curvature, as it greatly influences the bending process.
- Spring back increases with the radius of curvature.
- Spring back decreases with a decrease in the radius of curvature.
- The plate thickness should generally be below a certain limit, with consideration given to the Z-small curvature radius of the bending sheet.
Further reading: Solutions for Spring Back of Metal Stamping Parts
Effective Solutions to Overcome Bending Problems
To eliminate or minimize the bending problem in metal stamping, it is crucial to implement appropriate measures at the bending step of the stamping parts manufacturing process. Here, we present a comprehensive guide to help you address this issue effectively.
-
Optimizing Punch and Die Gaps to Minimize Spring Back
The gap between the punch and the die plays a crucial role in determining the accuracy of the bending process. An improper gap can lead to poor fitment or undesired deformation. It is important to strike a balance between the punch and die gaps to minimize spring back and achieve precise bending results.
- When the gap between the punch and the die is larger than the plate thickness, the sheet cannot fit properly on the punch.
- A larger fillet radius of the punch increases the amount of spring back, while a smaller gap may eliminate spring back but result in inward slope deformation.
- To optimize results, the gap is generally set to be 0.02-0.05mm smaller than the plate thickness.
-
Selecting Appropriate Fillet Radii for Optimal Bending
The fillet radius at the shoulder of the die significantly affects the outcome of the bending process. Choosing an appropriate fillet radius is crucial to avoid outward or inward tilting of the part.
- A fillet radius that is too large leads to an outward opening of the part.
- A fillet radius that is too small causes inward tilting of the part.
- Generally, a fillet radius ranging from 2 to 4 times the plate thickness is selected to achieve optimal bending results.
-
Ensuring Adequate Bending Depth for Desired Shapes
The bending depth and the inner and outer openings of the bent part are essential considerations to achieve desired shapes and avoid unintended deformations.
- A small bending depth and large inner and outer openings result in the decreased outward opening as the depth increases.
- To ensure satisfactory results, the bending depth should be more than 4 times the plate thickness.
Quality Control and Inspection
Implement a robust quality control system throughout the metal stamping process. Regularly inspect the stamped components for any signs of bending or surface imperfections. Employ advanced measurement techniques, such as coordinate measuring machines (CMMs), to ensure dimensional accuracy and consistency.
Automated Visual Industrial Quality Control System
Further reading: Automated Visual Industrial Quality Control Systems for Precision Stamping Parts Manufacturing
Conclusion
By understanding the intricate details of metal stamping processing and optimizing the various factors involved, we can achieve precise bending outcomes while minimizing the effects of spring back. Implementing these insights into our metal stamping processes will contribute to enhanced product quality, reduced rework, and improved overall efficiency.
Metal stamping is a complex field, and every situation may require specific adjustments and considerations. By continuously refining your bending techniques based on practical experience and the principles outlined here, we can excel in metal stamping and outperform in the quest for high-quality, accurately shaped products.
Further reading: Cracking of metal stamping parts
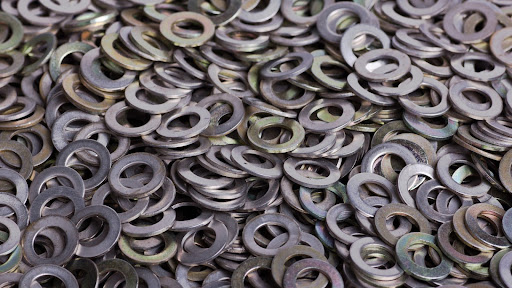
In the world of manufacturing and engineering, where precision reigns supreme, every component contributes to the final product's functionality, safety, and efficiency. Often overlooked yet essential, precision metal shims play a vital role.
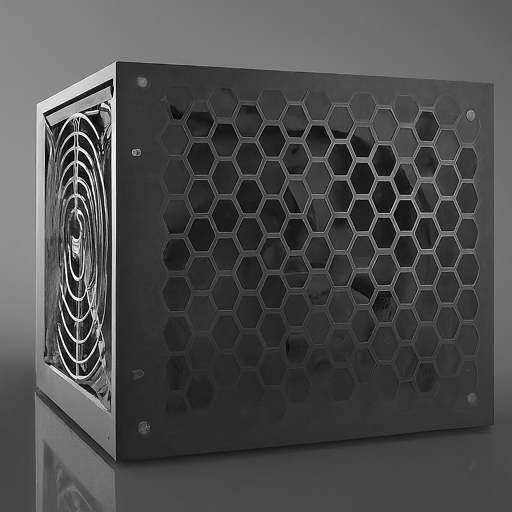
In the world of electronics, power supply units (PSUs) play a critical role in converting electrical energy, ensuring devices receive the correct voltage and current for optimal operation. To safeguard their components and manage heat, PSUs require durable and efficient enclosures. This is where metal stamped power supply shells excel.
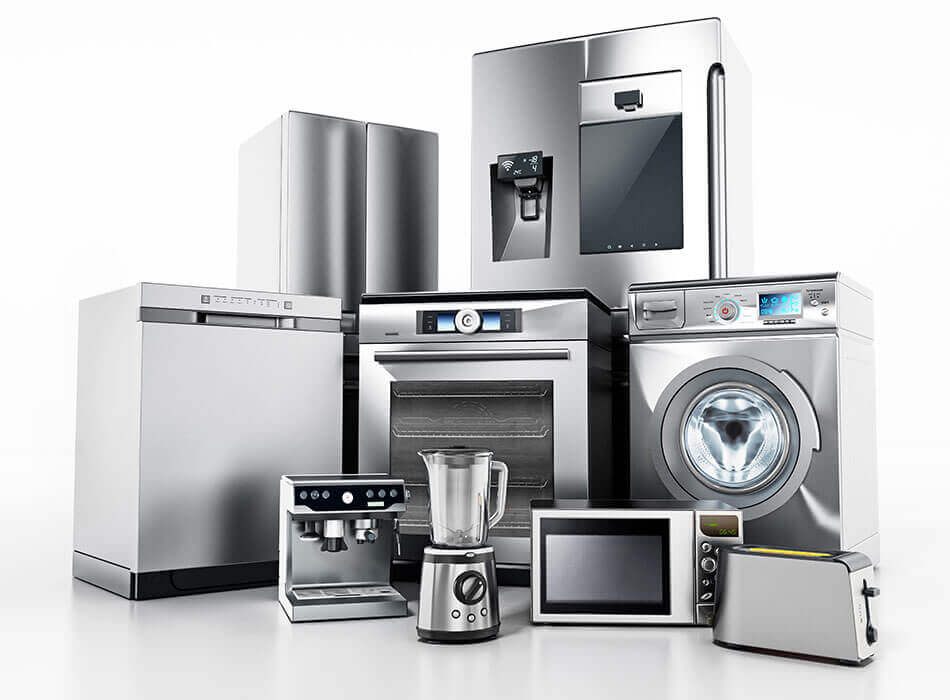
Custom-stamped appliance components are the backbone of products we rely on daily, from refrigerators to washing machines. To ensure appliances work efficiently and safely, these components must be manufactured to precise specifications. This involves challenges such as ensuring accurate dimensions and choosing materials with the right properties for each part.