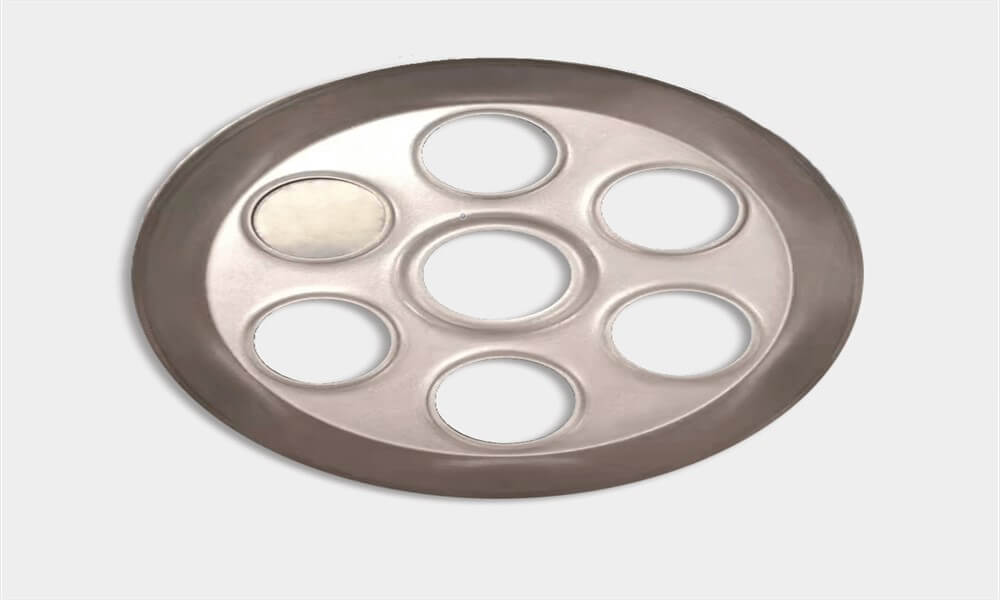
Metal stamping is a popular manufacturing process for producing high-precision metal parts with complex geometries. However, one common issue that metal stampers face is spring back, which is the elastic recovery of the material after being deformed by the stamping dies. Spring back can cause dimensional and shape deviations from the desired specifications, leading to quality problems and increased production costs. In this article, we present some effective solutions for reducing or eliminating spring back in metal stamping parts.
Understanding the Causes of Spring Back
Before discussing the solutions, it is important to understand the root causes of spring back in metal stamping. The main factors that contribute to spring back include:
- Material properties: The elastic modulus, yield strength, and work-hardening behavior of the material affect its ability to resist deformation and recover from it.
- Die design: The geometry, clearance, and surface finish of the stamping dies influence the distribution and magnitude of the bending stresses in the part.
- Process parameters: The blank holding force, punch force, and speed of the stamping press affect the strain and strain rate of the material during forming.
Solutions for Spring Back Reduction
Based on the above factors, several methods can be employed to reduce the spring back of metal stamping parts. These include:
Material Selection and Preparation
Choosing the right material and optimizing its properties can significantly reduce the spring back effect. Some tips to consider are:
- Use high-strength materials with low elastic moduli, such as advanced high-strength steels (AHSS), aluminum alloys, or titanium alloys.
- Preheat the material to increase its ductility and reduce its yield strength, especially for thick or cold-rolled sheets.
- Control the material thickness and uniformity to minimize the variation of strain distribution in the part.
Die Design and Maintenance
The stamping dies play a crucial role in determining the shape and quality of the stamped parts. To minimize spring back, the following aspects should be taken care of:
- Use a larger bending radius or a more gradual curve in the die profile to reduce the bending stress and distribute it more evenly.
- Apply a proper amount of clearance between the punch and the die to avoid material sticking and improve the material flow.
- Polish the die surfaces to minimize friction and wear, and apply lubrication to enhance the formability and reduce the galling.
Process Control and Optimization
Controlling and optimizing the stamping process parameters can also help reduce the spring back and improve the part quality. Some key measures to consider are:
- Adjust the blank holding force to prevent the material from slipping or wrinkling, and ensure a proper gap between the blank holder and the die surface.
- Increase the punch force or the forming speed to increase the strain rate and reduce the elastic recovery.
- Adopt a multi-stage or progressive forming process to distribute the deformation more evenly and reduce the residual stresses.
Conclusion
In summary, spring back is a common challenge in metal stamping, but it can be mitigated by implementing the right material, die, and process strategies. By selecting suitable material properties, optimizing the die design and maintenance, and controlling the process parameters, the spring-back effect can be reduced or even eliminated, leading to higher quality and more cost-effective metal stamping parts.
For more information or assistance with your metal stamping needs, feel free to contact us anytime.
Further reading: Cracking of metal stamping parts
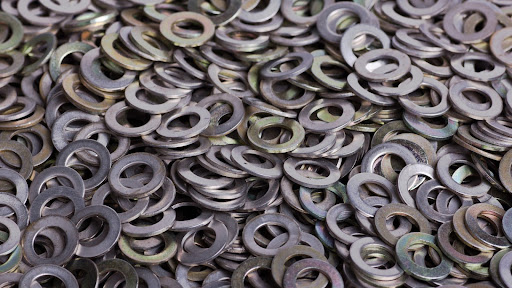
In the world of manufacturing and engineering, where precision reigns supreme, every component contributes to the final product's functionality, safety, and efficiency. Often overlooked yet essential, precision metal shims play a vital role.
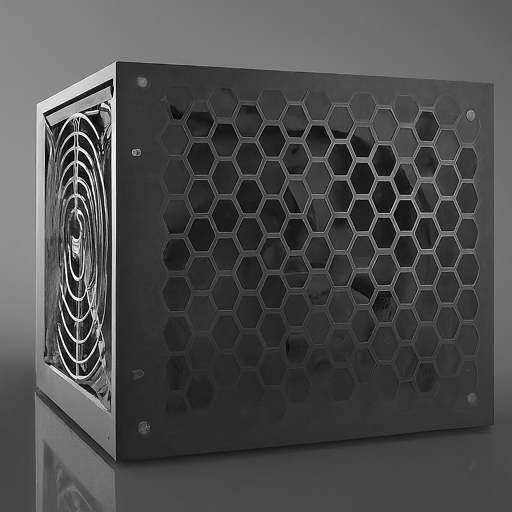
In the world of electronics, power supply units (PSUs) play a critical role in converting electrical energy, ensuring devices receive the correct voltage and current for optimal operation. To safeguard their components and manage heat, PSUs require durable and efficient enclosures. This is where metal stamped power supply shells excel.
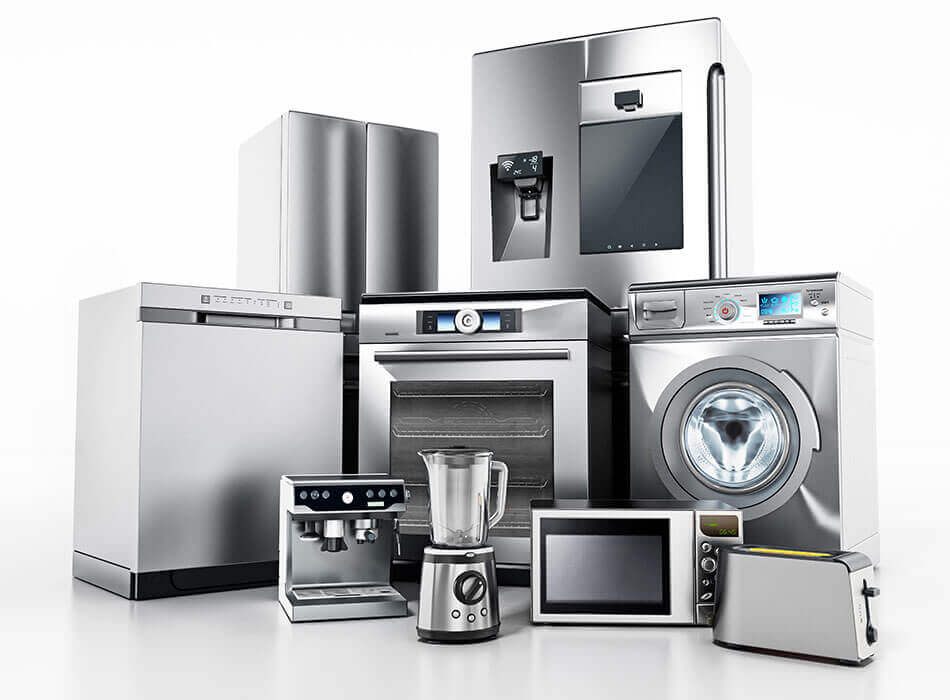
Custom-stamped appliance components are the backbone of products we rely on daily, from refrigerators to washing machines. To ensure appliances work efficiently and safely, these components must be manufactured to precise specifications. This involves challenges such as ensuring accurate dimensions and choosing materials with the right properties for each part.