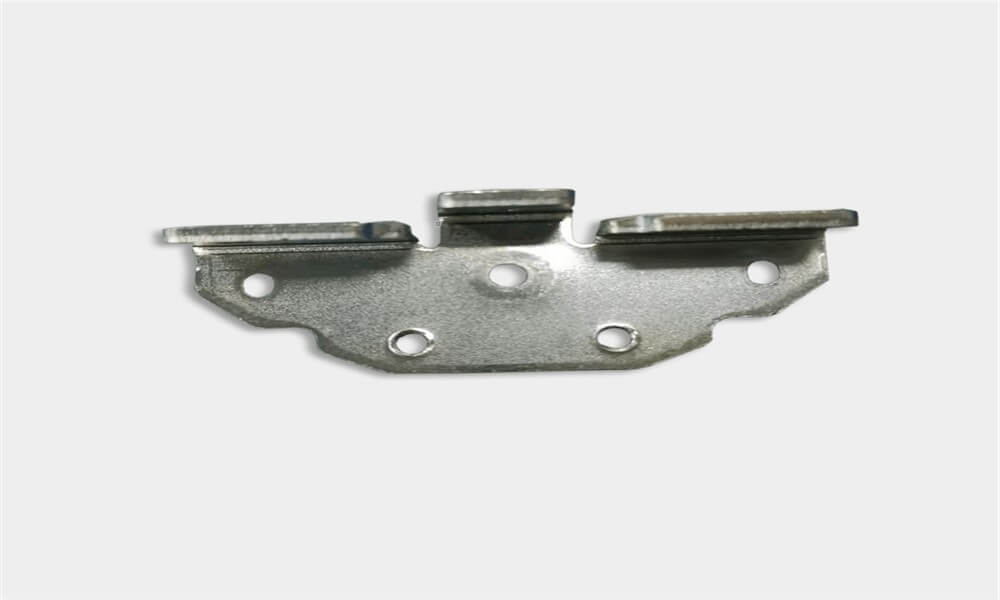
Metal stamping is a common manufacturing process that involves forming flat metal sheets into various shapes and sizes. The process can produce high-quality and consistent metal parts with precise dimensions and tolerances that are widely used in daily life. In this article, we will discuss the process characteristics of metal stamping parts and how they are manufactured.
Overview of the Metal Stamping Process
Metal stamping is a process that involves a series of operations to transform flat metal sheets into complex shapes and sizes. The process includes cutting, bending, stretching, and punching the metal sheet with a stamping press. The stamping press applies pressure to the metal sheet using a die and punch set, which creates the desired shape of the metal part.
The process can be performed on various types of metals, including steel, aluminum, copper, and brass. The thickness of the metal sheet used in the process can range from thin foils to thick sheets.
-
Hardware: parts produced from steel or some rare metals, production, and processing methods: cold/hot stamping, extrusion, extrusion, electric welding, and drilling, these also include other processing techniques, which are widely defined.
(Further reading: Hardware in Hardware Parts Processing) -
Stamping parts: It is widely used in hardware processing, which means that under the indoor temperature standard, material plates such as steel or rare metals pass through the mold, and are produced and processed by the press to form a metal product with a specific shape under the pressure of the machine.
Generally speaking, stamping parts generally refer to cold stamping parts. For example, if you want to turn a stainless steel sheet into a disc, you must first design a set of molds. The work surface of the mold is the plate. It looks like, pressing the stainless steel plate with a mold will turn it into the disc you want. This is cold stamping, which is immediately using a mold to stamp the hardware material. - Precision shrapnel stamping parts: That are widely used in all walks of life in our daily life, including some electronic components, auto parts, and architectural decoration materials.
Process Characteristics of Metal Stamping Stamping
There are several process characteristics of metal stamping parts that make it an ideal manufacturing process for producing high-quality metal parts. These characteristics include:
-
Precision
Metal stamping can produce highly precise and accurate metal parts with tight tolerances. The process can be controlled to achieve the desired dimensions and shapes of the metal part.
The product quality is stable and the interchangeability is good. The metal stamping die is used to form the product. There are a few factors affecting the change in product quality and the degree of harm is low. Some factors can be corrected by taking appropriate measures so that the quality of the product is controlled within the ideal range, and the stability of the product quality can effectively ensure its interchangeability. Good interchangeability is the basic guarantee for mass production of the assembly line. At the same time, it is also conducive to the maintenance and replacement of products.
-
Efficiency
Metal stamping is an efficient manufacturing process that can produce large quantities of metal parts in a short time. The process can be automated to increase production rates and reduce labor costs.
The number of parts or process content completed per unit of time is several times higher than that of ordinary processing methods, even hundreds of times. Moreover, the metal stamping process can further improve production efficiency by using one mold with multiple pieces and multiple process contents combined processing on a set of molds.
-
The high utilization rate of materials
Through different layout methods, such as cross, oblique, multi-row, mixing, nesting, and even non-waste layout, the utilization rate of materials can be effectively improved and the material cost of products can be reduced.
The material does not need to be heated. Under normal circumstances, the material does not need to be heated during the stamping operation. This can not only save energy, reduce the occupation of heating equipment and space, but also avoid the unstable shape and size of products caused by surface oxidation, burns, and deformation caused by heating. It is also possible to prevent adverse effects on the mold due to temperature rise.
-
Consistency
Metal stamping can produce consistent metal parts with uniform shapes and sizes. The process can be repeated to produce identical metal parts with the same dimensions and tolerances.
The product quality is stable and the interchangeability is good. The metal stamping die is used to form the product. There are a few factors affecting the change in product quality and the degree of harm is low. Some factors can be corrected by taking appropriate measures so that the quality of the product is controlled within the ideal range, and the stability of the product quality can effectively ensure its interchangeability. Good interchangeability is the basic guarantee for mass production of the assembly line. At the same time, it is also conducive to the maintenance and replacement of products.
-
Versatility
Metal stamping can be used to produce a wide range of metal parts with different shapes and sizes. The process can be customized to meet the specific requirements of each metal part.
-
Mechanical properties
The mechanical properties of punching parts are improved. Affected by the hardening phenomenon of metal stamping, the surface structure of punching parts is tight, the hardness and wear resistance is increased, and the strength and rigidity of punching parts are also improved.
-
Wide range of applications
There are many products suitable for stamping and forming. It can solve many processing contents that cannot or are difficult to be completed by general machining, especially for the processing and forming of some thin, soft, difficult, strange, micro parts, or parts of non-metallic materials, metal stamping forming is almost only one method of processing and forming.
Manufacturing Process of Metal Stamping Parts
The manufacturing process of metal stamping parts involves several steps, including:
- Design: The first step in the process is to design the metal part using computer-aided design (CAD) software. The design includes the dimensions, shape, and tolerances of the metal part.
- Tooling: The next step is to create the tooling for the stamping press. The tooling includes the die and punch set that will be used to shape the metal part.
- Material preparation: The metal sheet used in the process is prepared by cleaning and lubricating it to prevent scratches and damage during the stamping process. Various metals and alloys can be used in the metal stamping process, including Steel, Stainless steel, Aluminum, Brass, Copper, Nickel, Zinc, etc.
- Stamping: The metal sheet is then fed into the stamping press, where the die and punch set is used to shape the metal part. The process can be repeated to produce multiple identical metal parts.
- Finishing: After the metal part is stamped, it undergoes finishing operations such as deburring, polishing, and coating to improve its appearance and protect it from corrosion.
Production testing after stamping die development
Conclusion
The metal stamping process is a cost-effective, efficient, and versatile way to produce high-quality metal components in large volumes. The process involves several steps, including design, material selection, cutting, forming, and quality control. Proper maintenance and safety precautions are essential for the longevity and safety of the stamping equipment. The future of metal stamping process is expected to include more advanced technologies and materials.
If you have any metal stamping needs or questions, welcome to contact us. We look forward to hearing from you and helping you take your products to the next level.
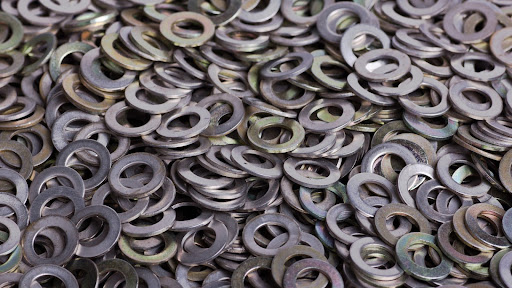
In the world of manufacturing and engineering, where precision reigns supreme, every component contributes to the final product's functionality, safety, and efficiency. Often overlooked yet essential, precision metal shims play a vital role.
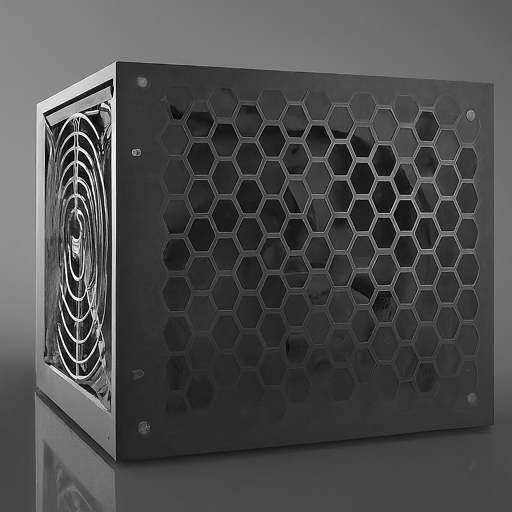
In the world of electronics, power supply units (PSUs) play a critical role in converting electrical energy, ensuring devices receive the correct voltage and current for optimal operation. To safeguard their components and manage heat, PSUs require durable and efficient enclosures. This is where metal stamped power supply shells excel.
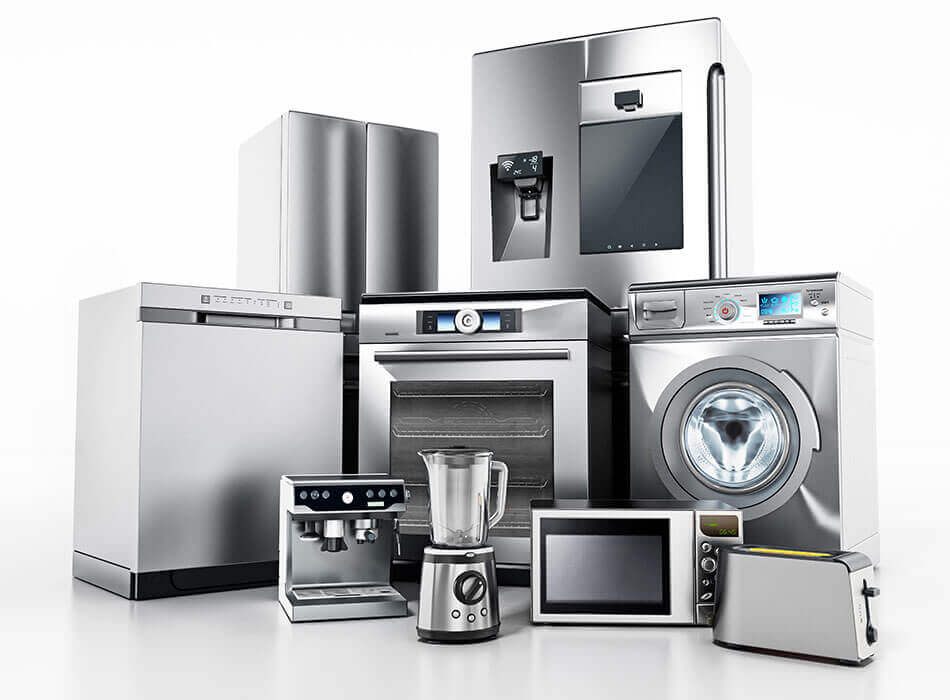
Custom-stamped appliance components are the backbone of products we rely on daily, from refrigerators to washing machines. To ensure appliances work efficiently and safely, these components must be manufactured to precise specifications. This involves challenges such as ensuring accurate dimensions and choosing materials with the right properties for each part.