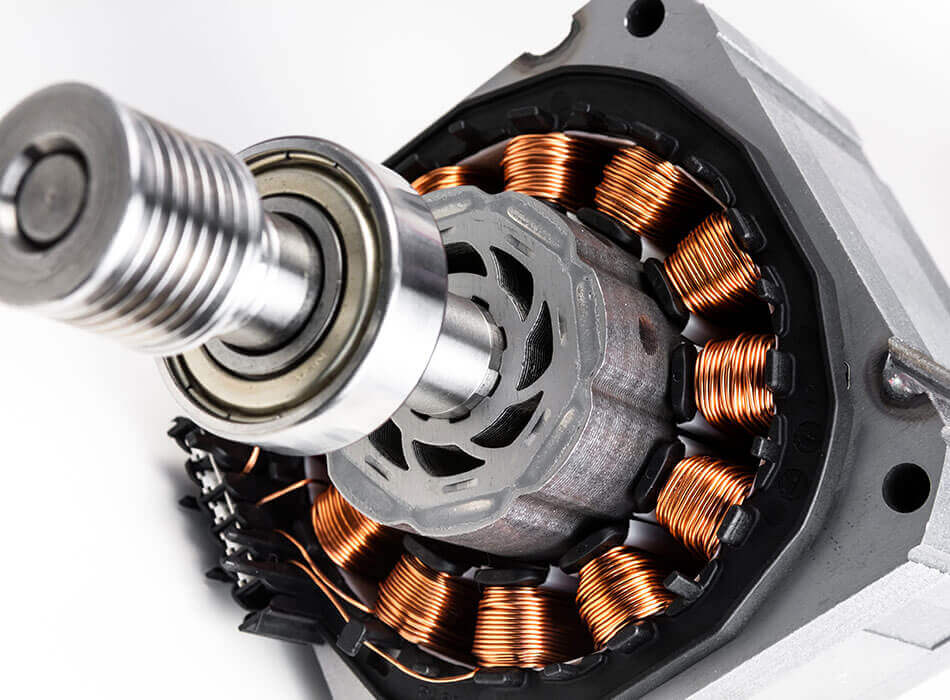
Differences between maglev fans and general fans
Maglev fans, also known as magnetic levitation fans, use the principle of magnetic levitation to suspend the fan blades in mid-air, reducing friction and allowing the fan to run more smoothly and quietly. In contrast, traditional fans use mechanical bearings to support the fan blades, which can create more noise and wear over time.
Another key difference between maglev fans and traditional fans is their energy efficiency. Maglev fans use less energy to operate because they don't require the mechanical bearings that traditional fans do. This can result in lower electricity costs over time.
A maglev fan typically includes the following components:
- Permanent magnets: These are used to create the magnetic field that suspends the fan blades.
- Electromagnets: These are used to control the movement of the fan blades.
- Fan blades: These are typically made of lightweight materials such as plastic or composite materials to reduce the weight and increase the efficiency of the fan.
- Power supply: This provides the necessary power to operate the electromagnets and control the movement of the fan blades.
On the other hand, a traditional fan typically includes the following components:
- Motor: This provides the power to rotate the fan blades.
- Bearings: These support the motor and allow it to rotate smoothly.
- Fan blades: These are typically made of metal or plastic, and are attached to a central hub that rotates along with the motor.
- Power supply: This provides the necessary power to operate the fan.
The main difference in composition between the maglev fan and the traditional fan is the use of magnetic levitation technology in the maglev fan which eliminates the need for mechanical bearings and reduces friction, also traditional fan uses a motor to rotate the fan blades while maglev fan uses electromagnets to control the movement of the fan blades.
Overall, maglev fans offer several advantages over traditional fans, including lower noise levels, increased energy efficiency, and a more modern design. However, they also tend to be more expensive and require advanced technology to operate.
Maglev Fan Stamping
There have many parts of maglev fans that can be stamped, including the housing, blades, maglev sheets, and mounting brackets. Special attention should be paid to the stamping maglev sheet. When stamping the maglev sheet of a maglev fan motor, there are several key factors that should be considered to ensure proper performance and longevity of the fan:
- Material selection: The magnetic levitation sheet should be made of high-quality magnetic material with the appropriate magnetic properties for the specific design of the fan motor.
- Dimensional accuracy: The magnetic levitation sheet should be stamped to precise dimensions to ensure proper fit and function within the fan motor.
- Surface finish: The surface of the stamped magnetic levitation sheet should be smooth and free of defects to minimize friction and ensure smooth movement of the fan blades.
- Stack-up tolerance: Stack-up tolerance is critical for magnetic levitation, it should be controlled to the lowest level possible to ensure the best levitation performance.
- Magnetic orientation: The orientation of the stamped magnetic levitation sheet should be carefully controlled to ensure that the magnetic fields are properly aligned for optimal levitation performance.
- Quality control: Inspection and testing should be performed during and after the stamping process to ensure that the magnetic levitation sheet meets all requirements and specifications.
It's important to mention that the stamping process of magnetic levitation sheets is a delicate process that requires a high level of precision and control, it's better to use specialized equipment and experienced technicians to ensure the best results.
Maglev Sheet Stamping for Maglev Fan
The most common materials used for Maglev Sheet Stamping are aluminum and steel, but other materials such as copper and titanium can also be used. The process may vary slightly depending on the specific metal being used.
Feng-Yu Precision Electronics Co., Ltd. is a China custom metal stamping manufacturer that was founded in 1971, based on our mastery of precision hardware processing technology and nearly 50 years of experience. Hardware processing provides key components for many industrial equipment and products, such as processing hardware stamping parts, injection molding parts, automotive stamping parts, precision hardware stamping parts, medical devices stamping, and other products. Our company provides a one-stop service process from drawing receiving to sample delivery, with stable quality and commitment, please contact us.
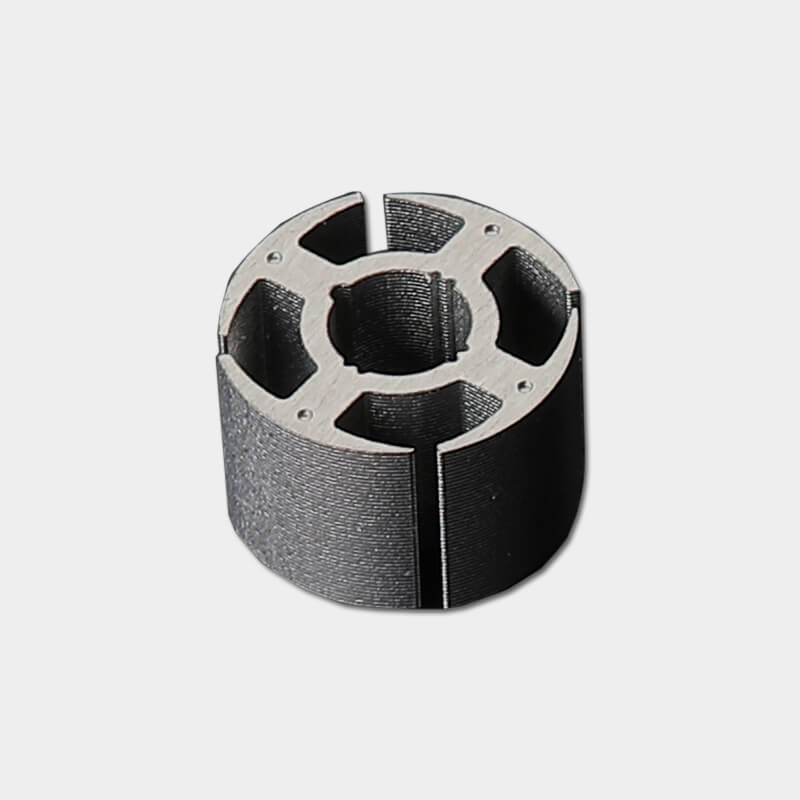
Metal stamping is essential for motor core manufacturing , providing precise shaping, high-volume production, and quality control measures.
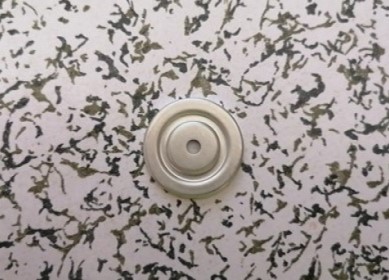
Metal stamping is essential for manufacturing pressure stabilizing gaskets, providing precise shaping, high-volume production, and quality control measures.
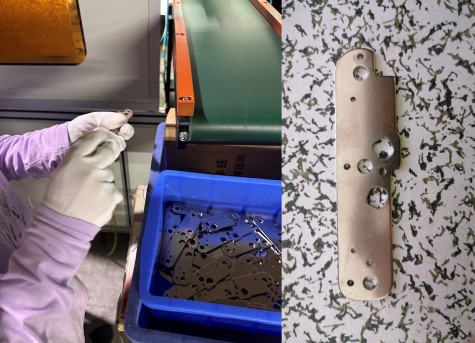
Metal stamping is crucial for producing stable, precisely positioned brackets in car audio systems. It offers cost-effective, high-quality manufacturing and adapts to advancements, including new materials, automation, and sustainability. Contact us for your precision metal stamping needs.