Electric motors are a critical component in many machines and appliances that we use every day. They convert electrical energy into mechanical energy, which powers the rotation of a shaft. A motor's efficiency and performance are dependent on its design, which includes various components like the rotor, stator, and motor housing. One critical component in motor design is motor stamping. In this article, we will explore what motor stamping is and how it works.
- What is Motor Stamping?
- How Does Motor Stamping Work?
- Types of Motor Stamping
- Importance of Motor Stamping
- Benefits of Motor Stamping
- Motor Stamping Techniques
- Material Selection for Motor Stamping
- Applications of Motor Stamping
- Conclusion
- Related Video of Motor Stamping
- Frequently Asked Questions(FAQs)
What is Motor Stamping?
Motor stamping, also known as laminated core stamping, is a process that involves manufacturing the stator and rotor cores of an electric motor or generator. The motor core is made up of several thin layers of magnetic steel, which are arranged and bonded together to create a solid core. The process of stamping involves punching out individual laminations from magnetic steel sheets and then assembling them together using a bonding adhesive.
How Does Motor Stamping Work?
Motor stamping works by creating a magnetic circuit within the motor's stator and rotor cores. The laminations used in motor stamping are made of a magnetic steel alloy, which provides a low resistance path for the magnetic flux to travel. The process of laminating the core reduces the eddy currents that can be generated during motor operation, improving the motor's efficiency.
The core stamping process starts with a coil of magnetic steel, which is unwound and then fed into a stamping press. The stamping press uses a die that is designed to cut the steel into specific shapes and sizes. The press applies pressure to the steel, creating the laminations needed for the motor core. The individual laminations are then stacked and bonded together using an adhesive material to create a solid core.
Types of Motor Stamping
There are two primary types of motor stamping used in motor manufacturing: lamination stamping and single-piece stamping.
-
Lamination Stamping
Lamination stamping is the most common type of motor stamping used in motor manufacturing. It involves creating the motor core by punching individual laminations from magnetic steel sheets and then bonding them together. This process creates a core that is made up of multiple layers of thin laminations, which reduces the core losses and increases the motor's efficiency.
-
Single Piece Stamping
Single-piece stamping, also known as solid core stamping, involves creating the motor core as a single solid piece. This process is more straightforward than lamination stamping, but it is less efficient due to the higher core losses generated during motor operation.
Importance of Motor Stamping
Motor stamping is a crucial process in motor design and manufacturing because it directly affects the motor's efficiency, durability, and performance. The motor's core is responsible for transferring the magnetic flux generated by the stator to the rotor, which produces the mechanical power needed to drive the motor.
A well-designed motor core with proper motor stamping can reduce core losses, increase efficiency, and enhance durability. Additionally, motor stamping can make the motor more cost-effective and improve the overall quality of the motor.
Benefits of Motor Stamping
There are several benefits of motor stamping, including:
-
Reduced Core Losses
Motor stamping reduces core losses by minimizing the eddy currents generated during motor operation. Eddy currents are induced currents that flow in the motor's core, which can cause energy loss and reduce the motor's efficiency. The use of laminated cores in motor stamping reduces the eddy currents, making the motor more efficient.
-
Improved Efficiency
Motor stamping increases the motor's efficiency by reducing energy loss and minimizing heat generation. The laminated core reduces the eddy currents generated during motor operation, which reduces energy loss and makes the motor more efficient.
-
Enhanced Durability
Motor stamping enhances the motor's durability by reducing the mechanical stress on the core. The laminated core reduces the core's mechanical stress, making the motor more robust and less susceptible to damage.
-
Cost-effective
Motor stamping can make the motor more cost-effective by reducing energy loss and increasing efficiency. A more efficient motor requires less energy to operate, which can reduce the overall operating cost of the motor.
Motor Stamping Techniques
There are several motor stamping techniques used in motor manufacturing, including:
-
Progressive Die Stamping
Progressive die stamping involves using a series of dies to create the laminations needed for the motor core. The steel is fed into the stamping press, which uses the dies to punch out the laminations. This process is highly automated and efficient, making it the preferred method for high-volume motor manufacturing.
-
Compound Die Stamping
Compound die stamping involves using a single die to create the laminations needed for the motor core. The die has multiple stations that perform different operations, such as cutting, punching, and bending. This process is less automated than progressive die stamping but is still efficient for low to medium-volume motor manufacturing.
-
Tandem Die Stamping
Tandem die stamping involves using two or more dies to create the laminations needed for the motor core. The steel is fed through multiple stamping presses, with each press performing a different operation. This process is less automated than progressive die stamping but is more efficient than compound dies stamping.
Material Selection for Motor Stamping
SUS 304 Stainless Steel: The Ideal Choice for Motor Bearings
When it comes to choosing the right material for motor bearings, SUS 304 stainless steel stands out as an exceptional option. Renowned for its remarkable combination of properties, SUS 304 is highly regarded in various industries for its corrosion resistance, heat resistance, low-temperature strength, and mechanical prowess.
SUS 304 is a type of austenitic stainless steel that contains chromium and nickel, which are essential elements for enhancing its corrosion resistance. This grade of stainless steel is widely used in different applications due to its outstanding performance and versatility.
-
Corrosion Resistance
One of the key factors that make SUS 304 an ideal choice for motor bearings is its exceptional resistance to corrosion. The chromium content in SUS 304 forms a protective oxide layer on the surface, preventing it from rusting even in harsh and corrosive environments. This property ensures the bearings maintain their integrity and performance over an extended period.
-
Heat Resistance
Motor bearings often operate under high-temperature conditions, and this is where SUS 304 truly shines. Its ability to withstand elevated temperatures without losing its structural integrity makes it a reliable material for bearings used in high-temperature applications.
-
Mechanical Properties
The mechanical properties of SUS 304 stainless steel play a crucial role in its suitability for motor bearings. It offers an excellent combination of tensile strength, yield strength, and elongation, providing bearings with the necessary durability and resilience.
-
No Heat Treatment Hardening Phenomenon
Unlike many other steel types, SUS 304 does not undergo heat treatment hardening. This eliminates the risk of brittleness and ensures that the bearings maintain their toughness and resistance to mechanical stress.
-
Non-Magnetic Properties
Another advantage of SUS 304 stainless steel is its non-magnetic nature, making it suitable for applications where magnetic interference is undesirable, such as certain medical equipment and electronic devices.
SUS 304 stainless steel undoubtedly reigns as an optimal choice for motor bearings. Its impressive corrosion resistance, heat resistance, and mechanical properties make it a highly sought-after material in various industries. With the ability to withstand challenging environments and maintain its performance over time, SUS 304 ensures the smooth operation and longevity of motor bearings in diverse applications.
SUS 430 Stainless Steel: The Ideal Choice for Motor Casings
When it comes to choosing materials for industrial applications, stainless steel has proven to be one of the most versatile and reliable choices. Among the various grades of stainless steel available, SUS 430 stands out for its unique properties, making it an ideal choice for specific applications, such as motor casings.
SUS 430 stainless steel is a ferritic grade of stainless steel containing 16-18% chromium, making it less resistant to corrosion than austenitic stainless steel but highly resistant to cracking. It is known for its outstanding toughness, formability, and heat resistance.
-
Low Thermal Expansion Rate
One of the most significant advantages of SUS 430 stainless steel is its low thermal expansion rate. When exposed to high temperatures, some materials tend to expand significantly, which can cause structural issues. However, SUS 430 exhibits minimal thermal expansion, ensuring stability and structural integrity, even under extreme heat conditions. This property makes it an excellent choice for components in motor casings that are subjected to varying temperatures during operation.
-
Good Oxidation Resistance
Another essential property of SUS 430 stainless steel is its excellent oxidation resistance. Oxidation is a chemical reaction that occurs when materials are exposed to oxygen and heat, leading to the formation of oxides. SUS 430's high chromium content allows it to form a protective layer that prevents oxidation and corrosion, making it suitable for applications where exposure to oxygen and heat is inevitable, such as motor casings.
SUS 430 stainless steel is a versatile and reliable material with a low thermal expansion rate and excellent oxidation resistance. These properties make it suitable for a wide range of applications, with motor casings being one of the most prominent beneficiaries. Its ability to withstand varying temperatures and exposure to oxygen makes it an ideal choice for protecting critical motor components.
Applications of Motor Stamping
Motor stamping is used in various applications, including:
-
Electric Motors
Motor stamping is used extensively in the manufacturing of electric motors. The motor core is responsible for transferring the magnetic flux generated by the stator to the rotor, which produces the mechanical power needed to drive the motor. The use of motor stamping in electric motors makes them more efficient and cost-effective.
-
Generators
Motor stamping is also used in the manufacturing of generators. Generators convert mechanical energy into electrical energy, and the motor core is an essential component in this process. The use of motor stamping in generators reduces energy loss and increases efficiency.
-
Transformers
Transformers use motor stamping in their design to transfer electrical energy from one circuit to another. The laminated core reduces energy loss and makes the transformer more efficient.
-
Solenoids
Solenoids use motor stamping in their design to create a magnetic field. The laminated core reduces energy loss and makes the solenoid more efficient.
Conclusion
Motor stamping is a critical process in motor design and manufacturing. It involves creating the stator and rotor cores of an electric motor or generator by punching out individual laminations from magnetic steel sheets and then bonding them together. Motor stamping reduces core losses, increases efficiency, enhances durability, and makes the motor more cost-effective. The different motor stamping techniques used in motor manufacturing include progressive die stamping, compound die stamping, and tandem die stamping, each with its advantages and applications. Motor stamping is used in various applications, including electric motors, generators, transformers, and solenoids, making it an essential process in the manufacturing industry.
Overall, the use of motor stamping can significantly improve the performance and efficiency of motors, generators, and transformers, reducing energy loss and making them more cost-effective. Motor manufacturers must carefully consider the motor stamping technique they use to ensure they create high-quality motors that meet customer needs and industry standards. If you have any motor stamping needs, welcome to contact us.
Related Video of Motor Stamping
Small Motor Casing Stamping - High Precision Manufacturing
Motor Magnetic Levitation Sheet Stamping - High Precision Manufacturing
Motor Stator Stamping
Frequently Asked Questions(FAQs)
What is the purpose of motor stamping?
Motor stamping is the process of creating the stator and rotor cores of an electric motor or generator by punching out individual laminations from magnetic steel sheets and then bonding them together. The purpose of motor stamping is to reduce core losses, increase efficiency, enhance durability, and make the motor more cost-effective.
What is the difference between progressive die stamping and compound die stamping?
Progressive die stamping involves using a series of dies to create the laminations needed for the motor core, while compound dies stamping involves using a single die to create the laminations. Progressive die stamping is more automated and efficient, making it ideal for high-volume motor manufacturing, while compound dies stamping is less automated but still efficient for low to medium-volume motor manufacturing.
What applications use motor stamping?
Motor stamping is used in various applications, including electric motors, generators, transformers, and solenoids.
How does motor stamping improve motor performance?
Motor stamping reduces core losses, minimizes heat generation, and enhances durability, making the motor more efficient and cost-effective.
What factors should motor manufacturers consider when selecting a motor stamping technique?
Motor manufacturers should consider the volume of motors they need to produce, the desired motor performance, and the cost-effectiveness of the motor stamping technique when selecting a motor stamping technique.
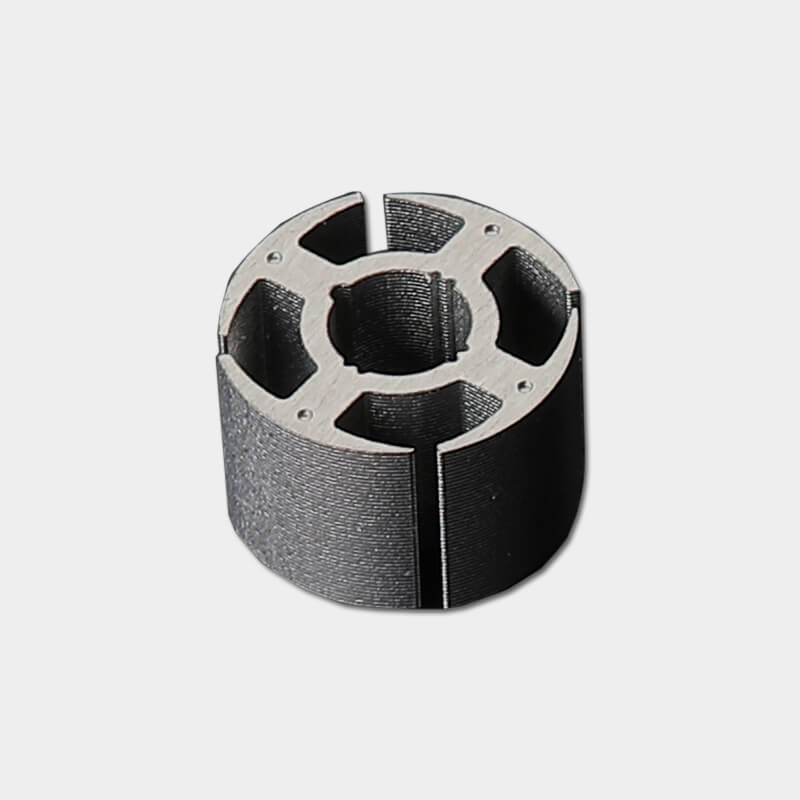
Metal stamping is essential for motor core manufacturing , providing precise shaping, high-volume production, and quality control measures.
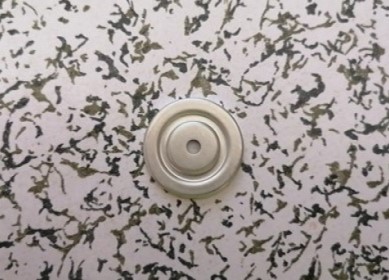
Metal stamping is essential for manufacturing pressure stabilizing gaskets, providing precise shaping, high-volume production, and quality control measures.
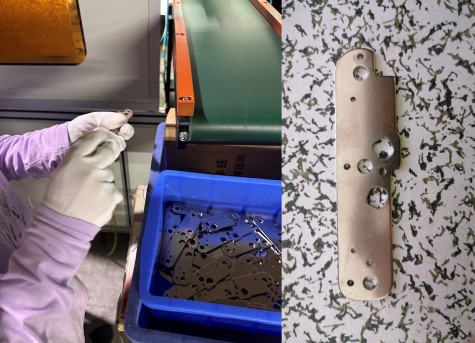
Metal stamping is crucial for producing stable, precisely positioned brackets in car audio systems. It offers cost-effective, high-quality manufacturing and adapts to advancements, including new materials, automation, and sustainability. Contact us for your precision metal stamping needs.