The challenges associated with metal stamping small parts can vary depending on the specific requirements and characteristics of the parts involved. However, some common challenges in metal stamping small parts include :
1. Tight Tolerances
One of the biggest challenges with stamping small metal parts is achieving tight dimensional tolerances and accuracy. The smaller the part, the more difficult it becomes to hold very tight tolerances across all features and dimensions. When tolerances get down to thousandths of an inch or less, the stamping process needs to be incredibly precise and repeatable in order to produce consistent parts within spec.
Any variations in the press, dies, material, lubrication, operator, etc. can easily push small parts out of tolerance specifications. Tighter tolerances leave less margin for error. Controlling the repeatability and precision of the stamping process is critical, but also more challenging and costly as tolerances get tighter. Improving process capabilities to hold very tight tolerances requires investment in high-end tooling and equipment. It also demands experience and expertise in how to optimize the process for micro-level precision and consistency when stamping small and intricate components.
2. Thin and Delicate Features
Stamping thin or delicate features like fins or tabs can be challenging. During the stamping process, thin metal features are prone to bending, warping, or breaking.
The material thickness is a key factor. Thinner material gauges lack rigidity and are more susceptible to deformation. Features that are too thin relative to surface area and unsupported length will tend to fold, wrinkle or fracture under stamping pressure and tool impacts.
Part geometry also plays a role. Narrow extensions, long unsupported spans, and complex cutouts place more stress on delicate areas. Tab connections must be properly designed to avoid tearing or shearing during the stamping stroke.
Fine-tuning parameters like die clearances, material type, press speed, and lubrication can help. But ultimately the part design needs to account for thinning and stamping stresses to successfully form thin, delicate features on small metal parts.
3. Part Geometry
Complex part geometries like ribs, bosses, holes, and other intricate features can present challenges in metal stamping small parts. The material flow in the stamping process can be impacted when pressing metal into these kinds of geometries.
Parts with many tight internal angles or radii often have trouble filling out properly. This can lead to areas of thin or incomplete material. Parts with an irregular shape may also have uneven material flow, causing distortion in the final part.
Holes, slots, and other voids in small stamped parts need to hold tight positional and dimensional tolerances. But the material flow and springback effects during stamping can shift these features out of position. Secondary operations are sometimes required to correct hole locations or bring slots into spec after stamping.
Bosses, ribs, and other protruding features can be prone to cracking or splitting during the stamping process. The quickly changing material flow puts stress on these delicate geometries. Extra care must be taken in the die design and stamping process to avoid splitting them. This may require things like specialized stamping sequences, draw beads, or venting channels in the die.
In general, the more complex the geometry, the more potential issues arise with material flow, distortion, part fracture, and holding tolerances in small stamped metal parts. Clever die design strategies and secondary finishing processes are often needed to produce complex small part geometries via metal stamping.
4. Material Properties
The material properties of metals used for small stamped parts can present challenges. Harder materials like high strength steel are more difficult to stamp without defects compared to softer metals like copper or aluminum. This is because high strength steels have greater springback and require higher stamping forces. Springback causes deviations from the intended part geometry. Higher stamping forces lead to greater tool wear.
Annealed materials are easier to stamp than work-hardened metals. But annealing adds cost and time to the manufacturing process. Surface finish requirements may limit the ability to anneal parts after stamping.
Grain structure also impacts formability. Materials with larger grains tend to have lower ductility. This makes them more prone to cracking during stamping. Small parts magnify these issues due to their thin cross-sections.
Coatings like galvanizing can impede metal flow during stamping. Lubricants suited for the material and coating must be used. Pre-coating small parts adds cost compared to post-coating after stamping.
The choice of material impacts nearly every aspect of stamping small parts. Engineering and metallurgy expertise is needed to select optimal materials and processes.
5. Lubrication Needs
Small parts have a higher surface area to volume ratio compared to larger parts. This increased surface area requires more lubricant during the stamping process to reduce friction between the dies and metal blank. Without adequate lubrication, the metal blank will stick to the stamping dies rather than flowing smoothly. This can lead to galling, tearing, or marking on the final parts.
Lubrication helps the blank metal slide cleanly through the stamping dies to achieve the desired part geometry. It also helps extend die life by reducing wear. Typical lubricants for stamping small parts include oil, wax, graphite, molybdenum disulfide, and others. The increased surface area of small parts means more lubricant must coat their surface to be effective. This increased lubrication need can add cost and processing considerations during metal stamping. Proper lubricant selection, application methods, and control are critical for producing quality small parts.
6. Handling Small Parts
One of the major challenges with metal stamping small parts is handling and manipulating the parts throughout the production process. After stamping, the small parts need to go through several secondary operations like heat treatment, plating, coating, etc. Typically, parts are loaded into baskets or totes and moved between processes. However, small parts can be difficult to manually handle.
Automated handling and sorting of small stamped parts presents challenges. Vibratory bowl feeders are commonly used, but these rely on the geometry of the part to function properly. Complex 3D geometries don't always move as expected through the feeder. Vision systems can help inspect and orient random parts, but integrating this automation adds cost. Small parts can also get stuck in transfer chutes due to static buildup.
Overall, handling and manipulating tiny metal stamped parts often requires specialized automation and handling equipment. Manual handling is tedious and can result in part damage or loss. Extra care needs to be taken to prevent scrap loss of small parts. Improving automation and implementing error-proofing can help optimize processes when working with small stamped components.
7. Scrap Rates
Stamping small, complex metal parts often results in higher scrap rates compared to larger, simpler parts. This is due to the tighter tolerances and more delicate features involved. When working with extremely small clearances or thin walls, even tiny variations in the process can lead to defects and scrapped parts.
The complex geometries that enable miniaturization and weight reduction also increase the likelihood of tearing, wrinkling, springback issues, and other defects during stamping. This further drives up scrap quantities. High scrap rates then negatively impact production costs and timelines.
Scrap minimization strategies are essential for small part stamping. Frequent inspection and measurement allows for early detection and correction of any process variations. Improved lubrication, stock selection, tooling, and operator training can also help reduce scrap. However, even with optimized processes, some level of increased scrap should be expected when stamping small, complex metal components.
8. Secondary Processing
Secondary processing steps like tapping holes or insert molding can present challenges when working with small stamped metal parts. The tiny size of the parts makes them difficult to handle and accurately position during secondary operations.
Small part sizes limit the amount of material that is available for creating threaded holes or inserting molded plastic components. There is less room for error in ensuring proper alignment. If a tapped hole or inserted component is slightly off, it can ruin the part or cause performance issues.
Automating secondary processing for small parts can help improve precision and repeatability. But the equipment needed for handling and manipulating miniature components can be an expensive investment. Manual secondary processing may be viable for lower volumes, but becomes challenging with higher production runs.
Extra diligence is required in handling, inspecting, and tracking small parts through all manufacturing steps. Parts can easily get lost, damaged, or mixed up if not controlled appropriately. Any defects from secondary processing are magnified on smaller parts.
Planning ahead for secondary processing needs during the part design stage is key. Building in features like integral molded components rather than secondary assembly can sidestep some of these small part challenges. But overall, secondary processing adds cost and complexity that must be weighed, especially with smaller parts.
In conclusion, "Part 1" of our exploration into the challenges of metal stamping miniature components has provided a detailed insight into the first eight hurdles faced by manufacturers in this precision-driven industry. From material considerations to technological intricacies, each challenge underscores the complexity and precision required in the production of these small yet critical components.
As we navigate through these challenges, it becomes evident that overcoming them demands a harmonious blend of advanced technology, meticulous process design, and the expertise of skilled craftsmen. The commitment to addressing these challenges positions manufacturers at the forefront of innovation and ensures the delivery of high-quality miniature components that meet and exceed industry standards.
Stay tuned for "10 Challenges of Metal Stamping Miniature Components (Part 2)," where we will delve into the final two challenges, accompanied by real-world case studies that highlight the practical applications of overcoming these obstacles. Join us as we continue our journey through the dynamic landscape of metal stamping, where challenges pave the way for innovation and excellence in miniature component manufacturing.
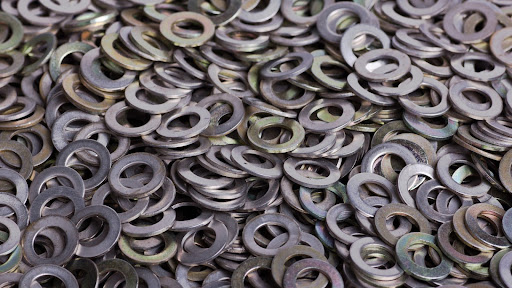
In the world of manufacturing and engineering, where precision reigns supreme, every component contributes to the final product's functionality, safety, and efficiency. Often overlooked yet essential, precision metal shims play a vital role.
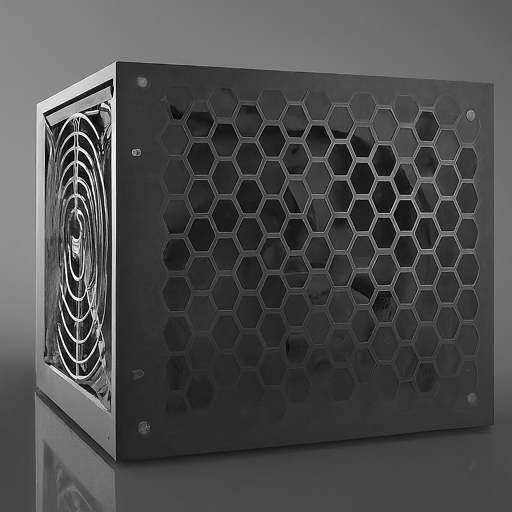
In the world of electronics, power supply units (PSUs) play a critical role in converting electrical energy, ensuring devices receive the correct voltage and current for optimal operation. To safeguard their components and manage heat, PSUs require durable and efficient enclosures. This is where metal stamped power supply shells excel.
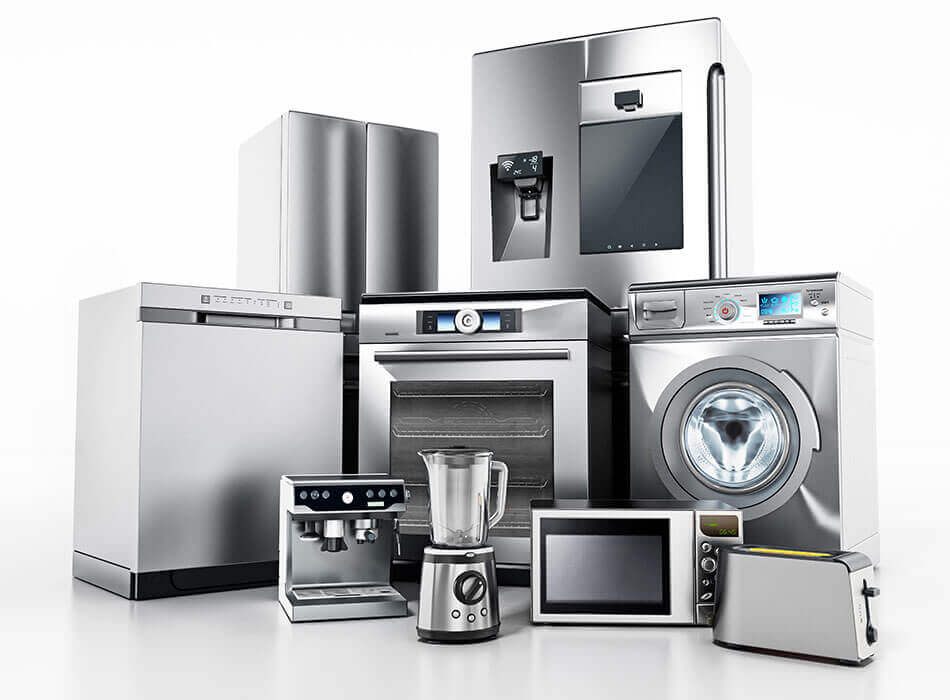
Custom-stamped appliance components are the backbone of products we rely on daily, from refrigerators to washing machines. To ensure appliances work efficiently and safely, these components must be manufactured to precise specifications. This involves challenges such as ensuring accurate dimensions and choosing materials with the right properties for each part.