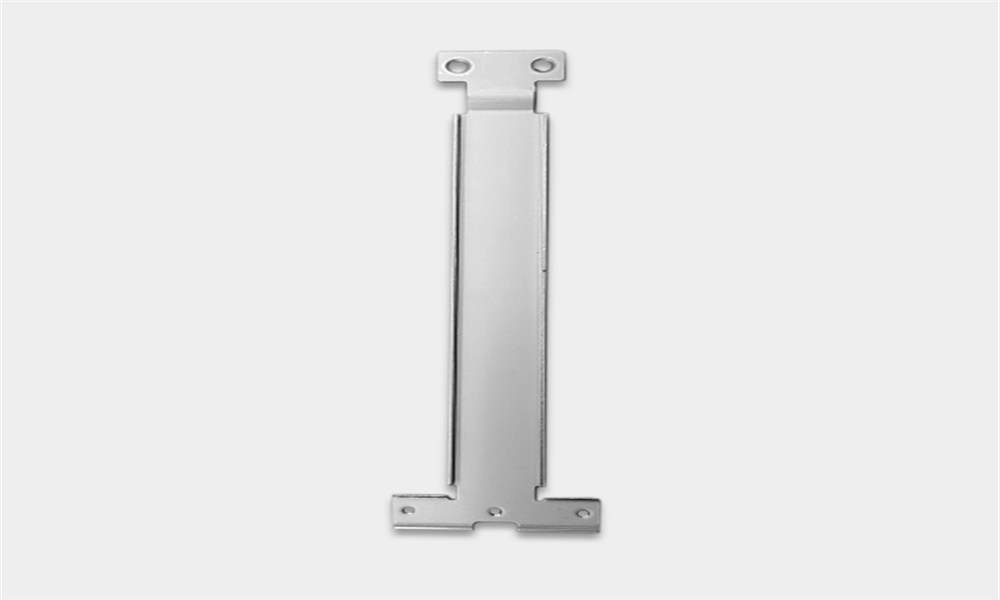
The advantages of metal stamping parts
- During metal stamping, the size and shape accuracy of metal stamping parts are guaranteed by the mold, which generally does not destroy the surface quality of the stamping parts, and the life of the mold is generally long, so the quality of metal stamping is stable.
- Metal stamping can produce parts with a wide range of sizes and complex shapes, such as stopwatches as small as clocks, as large as automobile longitudinal beams, covering parts, etc., plus the cold deformation hardening effect of the material during metal stamping, the strength of metal stamping and stiffness is high.
- The production efficiency of metal stamping is high, the operation is convenient, and it is easy to realize mechanization and automation. This is because metal stamping is done by punching dies and stamping equipment. The number of strokes of ordinary presses can reach dozens of times per minute, and the high-speed pressure can reach hundreds or even thousands of times per minute. It is possible to obtain a stamped part with only one stroke of the terminal.
- Metal stamping generally does not generate chips and scraps, consumes less material, and does not require other heating equipment, so it is a material-saving and energy-saving method, and the cost of metal stamping parts is low.
Factors affecting the accuracy of precision metal stamping parts:
- The quality of raw materials is poor.
- Due to the improper adjustment of the previous process or the wear of the rounded corners of the multi-process parts, the principle of equal volume during deformation is destroyed, causing the size change after blanking.
- Due to poor positioning during operation, or the positioning mechanism is not well designed, the blank moves during the blanking process. Or the inaccurate positioning caused by the defects of the shear parts (prism, missing edge, etc.) can cause the size to exceed tolerance.
- The blanking sequence is incorrect.
- The size of the die edge is out of tolerance 6. The spring back in the blanking process of precision metal stamping parts, the shape of the part in the previous process, and the shape of the supporting surface of the working part of the die in the next process are inconsistent, so the precision metal stamping parts are produced. Deformation occurs during the blanking process, and elastic recovery occurs after blanking, thus affecting dimensional accuracy.
- The shape of the plate is not good.
Further reading: Some Features of Metal Stamping Parts Processing
Feng-Yu is a China custom metal stamping manufacturer that was founded in 1971, based on our mastery of precision hardware processing technology and nearly 50 years of experience. Hardware processing provides key components for many industrial equipment and products, such as processing hardware stamping parts, injection molding parts, automotive stamping parts, precision hardware stamping parts, medical devices stamping, and other products. Our company provides a one-stop service process from drawing receiving to sample delivery, with stable quality and commitment, please contact us.
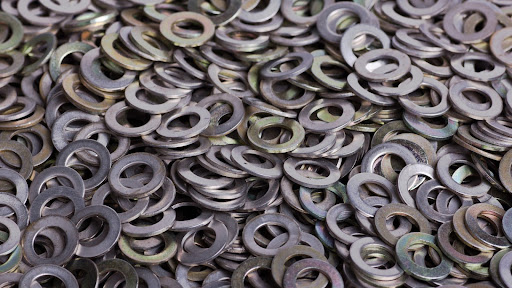
In the world of manufacturing and engineering, where precision reigns supreme, every component contributes to the final product's functionality, safety, and efficiency. Often overlooked yet essential, precision metal shims play a vital role.
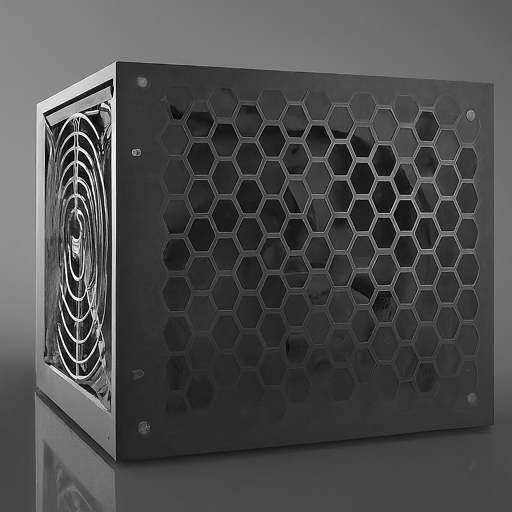
In the world of electronics, power supply units (PSUs) play a critical role in converting electrical energy, ensuring devices receive the correct voltage and current for optimal operation. To safeguard their components and manage heat, PSUs require durable and efficient enclosures. This is where metal stamped power supply shells excel.
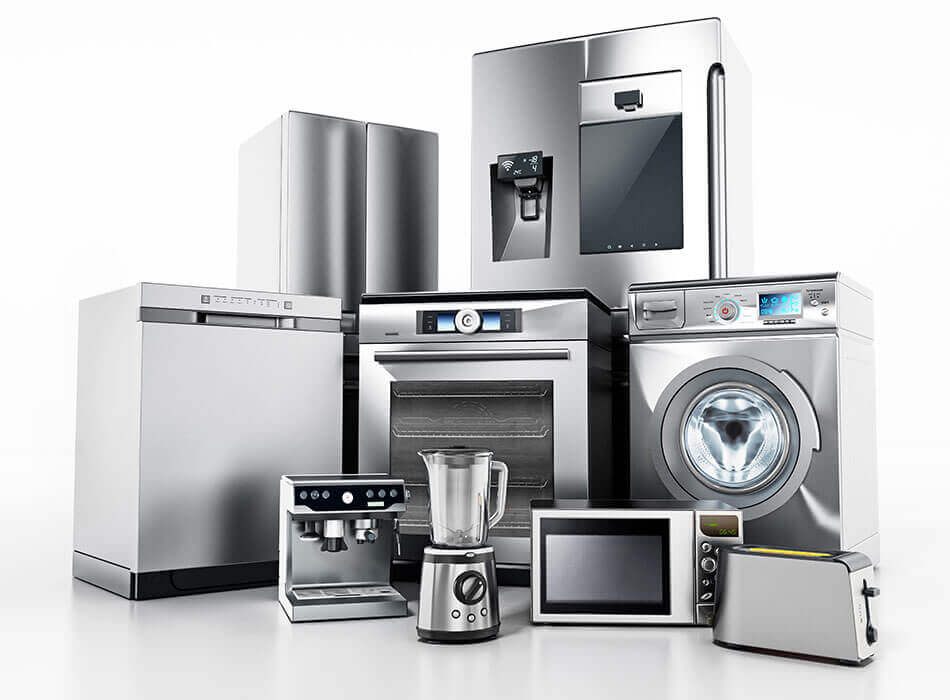
Custom-stamped appliance components are the backbone of products we rely on daily, from refrigerators to washing machines. To ensure appliances work efficiently and safely, these components must be manufactured to precise specifications. This involves challenges such as ensuring accurate dimensions and choosing materials with the right properties for each part.