Deep draw metal stamping is a sophisticated manufacturing process that enables the creation of intricate and complex metal components. This article delves into the world of deep draw metal stamping, exploring its process, materials, applications, advantages, and much more.
What is Deep Draw Metal Stamping
Deep draw metal stamping is a specialized metal forming technique that involves converting flat metal sheets into three-dimensional shapes. The process is particularly well-suited for producing parts with deep recesses or complex geometries, making it an essential method in various industries.
The Process of Deep Draw Metal Stamping
The process starts with a flat metal sheet placed over a die, followed by a punch that forces the metal into the die cavity. As the punch descends, the metal is stretched and bent, eventually taking the shape of the die. This deep drawing process can be repeated multiple times to achieve the desired part shape.
Here's an overview of the deep draw metal stamping process:
- Material Selection: The process typically begins with selecting the appropriate material, which is often a sheet or coil of metal such as steel, aluminum, stainless steel, or copper. The choice of material depends on the specific requirements of the part, including factors like strength, corrosion resistance, and cost.
-
Blanking: The first step is to cut the initial flat metal sheet or coil into a blank or disc that is slightly larger than the final desired shape of the part.
- Lubrication: To reduce friction and prevent damage to the metal, a lubricant or oil is applied to the surface of the blank and the tooling.
- Deep Drawing: The blank is placed in a die, which is a specialized tooling set that includes a punch and a die cavity. The punch is used to force the blank into the die cavity, which shapes the metal into the desired form. This process involves a series of progressive steps, with each step gradually forming the metal into a deeper shape.
- Redrawing: In some cases, multiple redraws may be necessary to achieve the desired depth and shape. Each redraw step refines the part's shape and increases the depth of the draw.
- Trimming: After the deep drawing process, excess metal (known as flash) may be present. This excess material is trimmed or cut off from the formed part to achieve the final dimensions.
- Additional Operations: Depending on the specific part requirements, additional operations such as piercing, flanging, and hole punching may be performed in subsequent steps.
-
Inspection: The finished parts are inspected for quality and dimensional accuracy to ensure they meet the required specifications.
Materials Used in Deep Draw Stamping
Deep draw stamping can be performed with various materials, including stainless steel, aluminum, brass, and more. The material choice depends on the specific requirements of the project, such as corrosion resistance, strength, or conductivity.
Advantages of Deep Draw Metal Stamping
- High precision and repeatability
-
Cost-effective for high-volume production
- Reduced material waste
- Suitable for a wide range of materials
- Complex shapes can be achieved
-
Improved material properties
Applications of Deep Draw Metal Stamping
Deep draw stamping finds applications in numerous industries, including automotive, aerospace, electronics, and medical. It is used to manufacture metal stamping parts like automotive fuel tank enclosures, electronic connectors, and medical device enclosures.
Deep Draw Stamping vs. Other Metal Forming Methods
Compared to other metal forming methods like CNC machining or die casting, deep draw stamping stands out for its efficiency, precision, and cost-effectiveness, especially in high-volume production scenarios.
Considerations for Design and Tooling
Successful deep draw stamping requires careful design and tooling considerations. Factors such as material selection, die design, and punch geometry play a critical role in the process's success.
Quality Control in Deep Draw Stamping
Quality control is paramount in deep draw stamping to ensure that each produced component meets the required specifications. Advanced inspection techniques are employed to maintain consistency and precision.
Environmental Sustainability
Deep draw stamping's reduced material waste and energy-efficient production processes contribute to environmental sustainability, making it a responsible choice for eco-conscious industries.
Challenges and Troubleshooting
While deep draw stamping offers numerous advantages, it also presents challenges, such as wrinkling or tearing of the material. Understanding these challenges and employing effective troubleshooting strategies is crucial.
Deep Draw Metal Stamping Service - Custom, Reliable
Feng Yu is a metal stamping parts manufacturer based in China and ISO 9001 certified, is your top choice for premium deep draw metal stamping solution. With nearly 50 years of experience in precision metal processing, we specialize in crafting high-quality, efficient, and reliable metal stamping solutions. Our state-of-the-art equipment and certified team guarantee that every products we manufacture meets rigorous quality standards. Trust Feng Yu for precision, quality, and innovation in stamping metal parts.
(Feng Yu's Business Partners)
Conclusion
In conclusion, deep draw metal stamping is a remarkable manufacturing process that has transformed the production of intricate metal components. Its advantages, applications, and sustainable qualities make it an indispensable part of modern manufacturing. Contact us now!
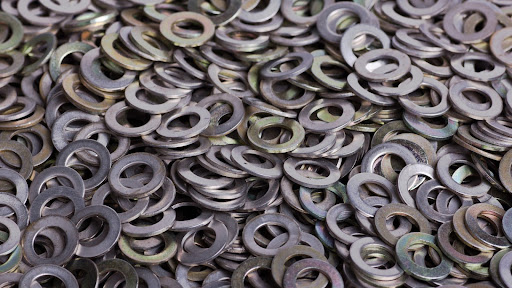
In the world of manufacturing and engineering, where precision reigns supreme, every component contributes to the final product's functionality, safety, and efficiency. Often overlooked yet essential, precision metal shims play a vital role.
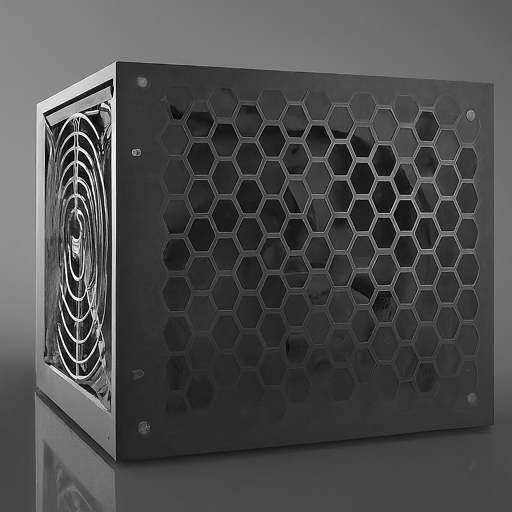
In the world of electronics, power supply units (PSUs) play a critical role in converting electrical energy, ensuring devices receive the correct voltage and current for optimal operation. To safeguard their components and manage heat, PSUs require durable and efficient enclosures. This is where metal stamped power supply shells excel.
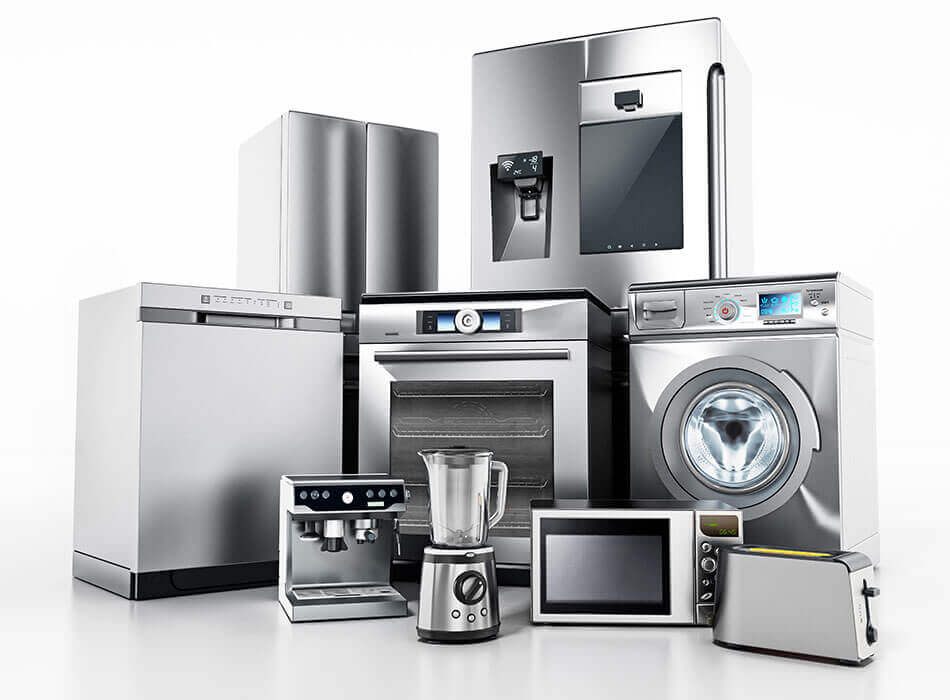
Custom-stamped appliance components are the backbone of products we rely on daily, from refrigerators to washing machines. To ensure appliances work efficiently and safely, these components must be manufactured to precise specifications. This involves challenges such as ensuring accurate dimensions and choosing materials with the right properties for each part.