Copper is a versatile metal that has been used for centuries for various applications. One of the popular applications of copper is in the manufacturing of electrical components, such as wires and connectors. Copper metal continuous stamping manufacturing is the process of creating copper components using a stamping press that operates continuously. This article will provide an in-depth understanding of copper metal continuous stamping manufacturing, its benefits, and its applications.
What is Copper Components Continuous Metal Stamping Manufacturing?
Copper components continuous metal stamping manufacturing is a process used to create copper components using a stamping press that operates continuously. The process involves feeding a strip of copper metal into the stamping press, which then cuts and shapes the metal into the desired shape. The stamping process is continuous, meaning that it operates without stopping, creating a high volume of components in a short amount of time.
Benefits of Copper Components Continuous Metal Stamping Manufacturing
There are several benefits to using copper metal continuous stamping manufacturing for creating copper components:
- High-efficiency:
-
Cost-effective:
Copper metal continuous stamping manufacturing is a cost-effective process that allows for the creation of components at a lower cost than other manufacturing processes. The process is automated, reducing the need for manual labor, and resulting in lower labor costs.
- High-precision:
Copper metal continuous stamping manufacturing is a highly efficient process that allows for the creation of a high volume of components in a short amount of time. The process is continuous, meaning that it operates without stopping, resulting in a fast turnaround time for production.
Copper metal continuous stamping manufacturing allows for the creation of components with high precision and accuracy. The stamping press can be programmed to cut and shape the metal to the exact specifications, resulting in components that are consistent in size and shape.
Process of Copper Components Continuous Metal Stamping Manufacturing
The copper metal continuous stamping manufacturing process involves several steps:
- Coil Preparation:
- Stamping:
- Inspection:
- Packaging:
The process begins with the preparation of a copper coil. The coil is fed into the stamping press, which then feeds the copper strip into the press.
The stamping process involves cutting and shaping the copper strip into the desired shape. The stamping press can be programmed to cut and shape the metal to the exact specifications.
After stamping, the copper components are inspected for defects or imperfections. Any defective components are removed from the production line.
The copper components are then packaged and prepared for shipping to customers.
The video showcases the entire process of copper components continuous metal stamping manufacturing from the preparation of the raw materials to the finished products. The process involves several stages, including designing the stamping tools, feeding the raw materials into the machine, and continuous stamping of the copper metal.
Brass Stamping and Galvanizing: Enhancing Corrosion Resistance and Solderability
Brass, a popular alloy composed of copper and zinc, finds extensive use in various industries due to its desirable properties such as durability, conductivity, and malleability. However, brass is prone to oxidation, which can lead to corrosion and hinder its performance. To address this issue, the process of passivation is employed after stamping and before galvanizing the brass surface. Passivation enhances the material's corrosion resistance and facilitates subsequent soldering to computer boards, ensuring optimal functionality and longevity.
Conduct secondary processes
To counteract the effects of oxidation and corrosion, passivation is a crucial step in the brass stamping and galvanizing process. Passivation involves treating the brass surface to create a protective layer that inhibits further oxidation and enhances its resistance to corrosion. This layer acts as a barrier between the brass and the environment, safeguarding it from moisture, chemicals, and other corrosive elements.
-
Passivation: Enhancing Corrosion Resistance
After the brass stamping process, passivation is applied to the surface. Passivation removes any surface contaminants or oxides formed during stamping and creates a protective layer. This layer prevents further oxidation and corrosion, improving the overall durability and lifespan of the brass component. Passivation treatments often involve the use of chemical solutions or electrochemical processes to ensure the effectiveness of the protective layer.
-
Galvanizing: Further Protection and Aesthetic Appeal
Following passivation, the next step is galvanizing. Galvanizing involves coating the passivated brass surface with a layer of zinc or zinc alloy. This process provides an additional layer of protection against corrosion, as zinc is more sacrificial and prone to oxidizing than brass. Moreover, galvanizing can enhance the aesthetic appeal of the brass component, providing a uniform and attractive finish.
-
Solderability: Facilitating the Connection to Computer Boards
In many industries, brass components require soldering to connect them to computer boards and other electronic devices. Passivation plays a crucial role in ensuring the solderability of brass. The passivated surface provides a clean and stable foundation for soldering, promoting proper adhesion and electrical conductivity. Without passivation, the oxidized brass surface would hinder the soldering process, leading to weak connections and potential failure.
Applications of Passivated Brass
Passivated brass finds applications in a wide range of industries. In the electronics industry, passivated brass components are used in connectors, terminals, switches, and computer components. The automotive industry utilizes passivated brass in electrical connectors, fuel systems, and engine components. Plumbing systems benefit from passivated brass fittings and valves, ensuring corrosion resistance and longevity.
Conclusion
In conclusion, brass, a versatile alloy, can be susceptible to oxidation and corrosion. To counteract these effects and ensure optimal performance, the brass stamping and galvanizing process incorporates passivation. Passivation enhances the corrosion resistance of brass, facilitating subsequent soldering to computer boards and improving overall functionality. The combination of passivation and galvanizing provides robust protection against environmental factors, prolonging the lifespan of brass components. As industries continue to rely on brass for its unique properties, passivation remains a critical step in maintaining its quality and longevity. If you have any questions or needs about copper stamping, welcome to contact us.
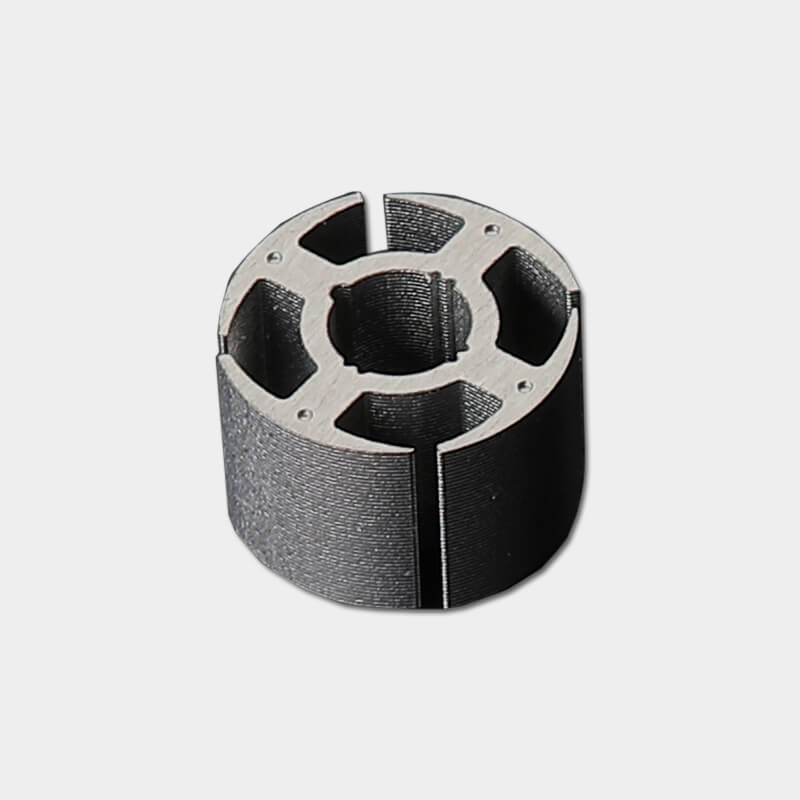
Metal stamping is essential for motor core manufacturing , providing precise shaping, high-volume production, and quality control measures.
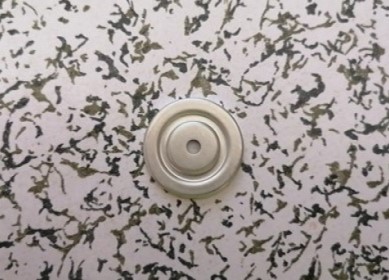
Metal stamping is essential for manufacturing pressure stabilizing gaskets, providing precise shaping, high-volume production, and quality control measures.
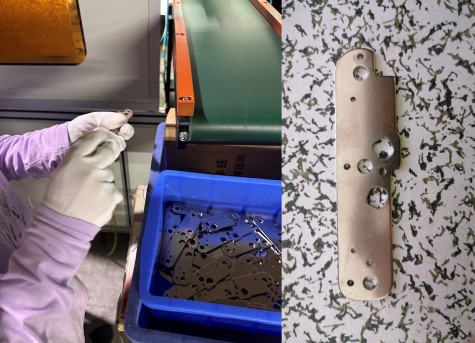
Metal stamping is crucial for producing stable, precisely positioned brackets in car audio systems. It offers cost-effective, high-quality manufacturing and adapts to advancements, including new materials, automation, and sustainability. Contact us for your precision metal stamping needs.