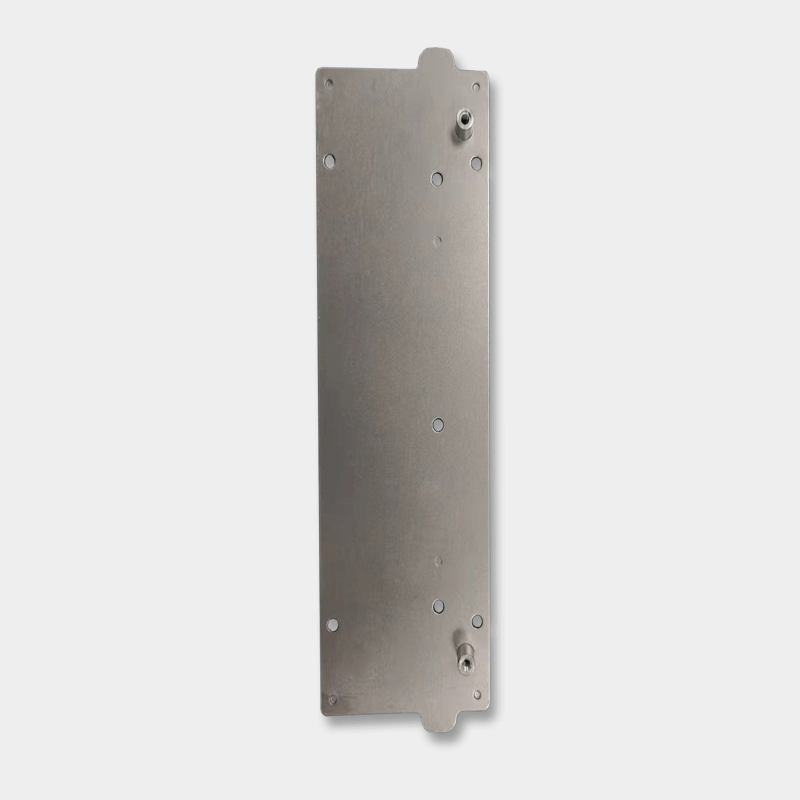
Sheet metal stamping is a widely used manufacturing process in the production of metal components for various industries. It involves the use of dies and presses to shape and cut metal sheets into the desired form. In this article, we will delve into the world of sheet metal stamping parts, exploring its applications, benefits, and the intricate process behind its creation.
What is Sheet Metal Stamping?
Sheet metal stamping is a manufacturing process that transforms flat metal sheets into various shapes and sizes. It involves the use of dies and presses to exert force on the metal, causing it to deform and take the desired form. This process is commonly used to create complex and precise components used in a wide range of industries.
The Advantages of Sheet Metal Stamping Parts
Sheet metal stamping offers several advantages over other manufacturing methods. First and foremost, it enables high-volume production at a rapid pace, making it a cost-effective option for mass-produced parts. Additionally, sheet metal stamping allows for tight tolerances and excellent repeatability, ensuring consistent quality in every piece.
The Sheet Metal Stamping Process
1. Preparation and Design
The sheet metal stamping process begins with thorough preparation and meticulous design. Engineers work closely to create detailed drawings and simulations to ensure the part's accuracy and feasibility.
2. Material Selection
Choosing the right material is crucial in sheet metal stamping. Different metals have varying properties, affecting the part's strength, durability, and corrosion resistance.
3. Die Design and Fabrication
Dies are specialized tools used in sheet metal stamping. Designing and fabricating the appropriate die is a crucial step to achieve the desired outcome.
4. Stamping Operations
The actual stamping process involves placing the metal sheet between the die's two halves and applying pressure using hydraulic or mechanical presses.
Common Applications of Sheet Metal Stamping Parts
1. Automotive Industry
Sheet metal stamping is widely used in the automotive sector to produce body panels, brackets, and structural components.
2. Aerospace Sector
Aerospace companies utilize sheet metal stamping for aircraft components such as wings, fuselage parts, and engine mounts.
3. Electronics and Electricals
The electronics industry relies on sheet metal stamping to manufacture enclosures, connectors, and heat sinks.
4. Household Appliances
Home appliances often incorporate stamped parts in their structures, enhancing their durability and functionality.
Factors Affecting Sheet Metal Stamping Quality
1. Material Thickness
The thickness of the metal sheet can impact the part's structural integrity and overall performance.
2. Lubrication
Proper lubrication is essential to prevent friction and ensure smooth stamping operations.
3. Press Speed and Force
The right balance of speed and force is crucial to achieving accurate and defect-free stamped parts.
4. Die Clearance
Optimal die clearance helps prevent material tearing and wrinkling during stamping.
Troubleshooting Common Issues in Sheet Metal Stamping
1. Wrinkling
Wrinkling occurs when the metal sheet buckles under pressure, affecting the part's appearance and integrity.
2. Springback
Springback is the tendency of the metal to return to its original shape after stamping, causing dimensional inaccuracies.
3. Tearing
Material tearing can occur due to improper die design or excessive force during stamping.
4. Burring
Burring is the unwanted formation of rough edges, requiring post-stamping deburring processes
FAQs (Frequently Asked Questions)
-
Is sheet metal stamping suitable for prototyping?
Yes, sheet metal stamping is commonly used for prototyping due to its speed and cost-effectiveness.
-
Which industries benefit the most from sheet metal stamping?
The automotive, aerospace, electronics, and appliance industries are among the primary beneficiaries of sheet metal stamping.
-
Can sheet metal stamping handle high-strength materials?
Yes, sheet metal stamping can accommodate high-strength materials such as stainless steel and titanium.
-
How is sheet metal waste managed?
Recycling and efficient material usage are employed to manage sheet metal waste responsibly.
-
What are the drawbacks of sheet metal stamping?
Some challenges include material springback, die wear, and tooling costs.
Conclusion
Sheet metal stamping parts play a pivotal role in various industries, enabling the creation of complex and durable components. This manufacturing process offers numerous advantages, such as cost-effectiveness and repeatability. With ongoing technological advancements, sheet metal stamping is poised to continue its contribution to the manufacturing world.
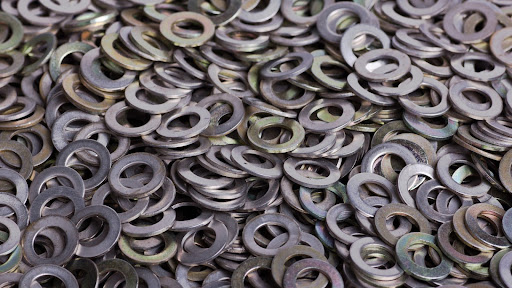
In the world of manufacturing and engineering, where precision reigns supreme, every component contributes to the final product's functionality, safety, and efficiency. Often overlooked yet essential, precision metal shims play a vital role.
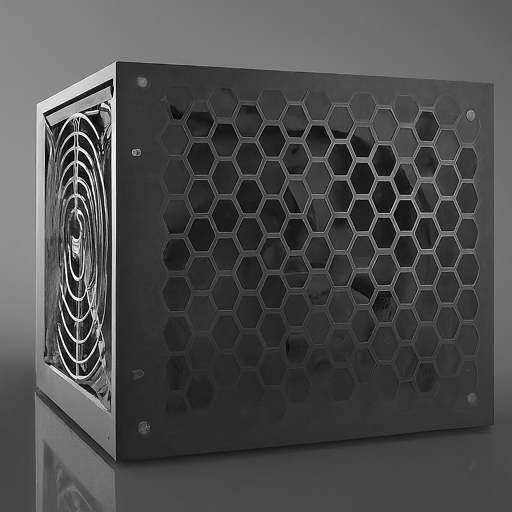
In the world of electronics, power supply units (PSUs) play a critical role in converting electrical energy, ensuring devices receive the correct voltage and current for optimal operation. To safeguard their components and manage heat, PSUs require durable and efficient enclosures. This is where metal stamped power supply shells excel.
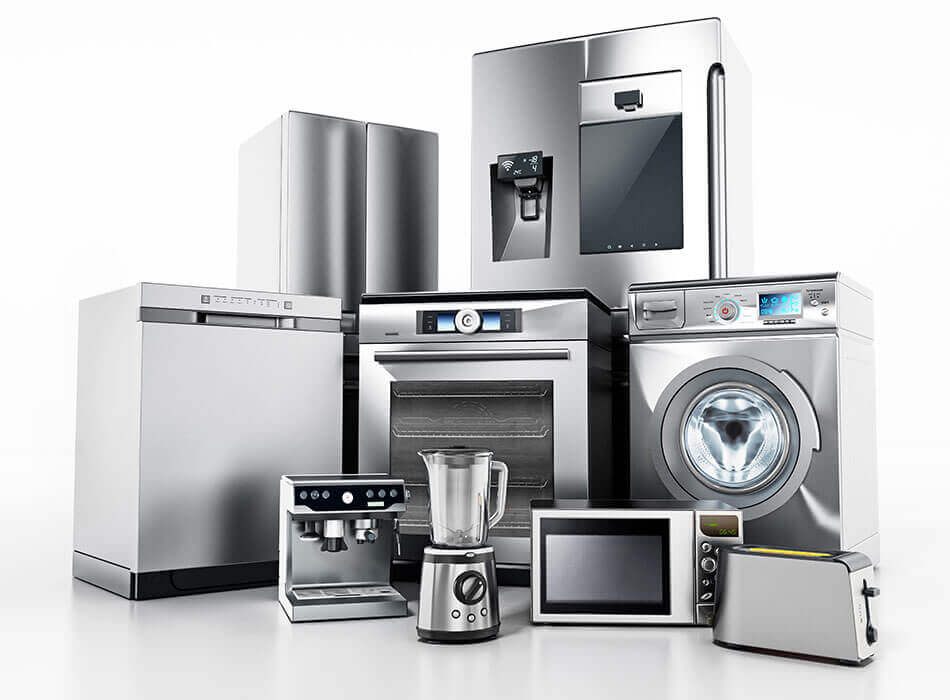
Custom-stamped appliance components are the backbone of products we rely on daily, from refrigerators to washing machines. To ensure appliances work efficiently and safely, these components must be manufactured to precise specifications. This involves challenges such as ensuring accurate dimensions and choosing materials with the right properties for each part.